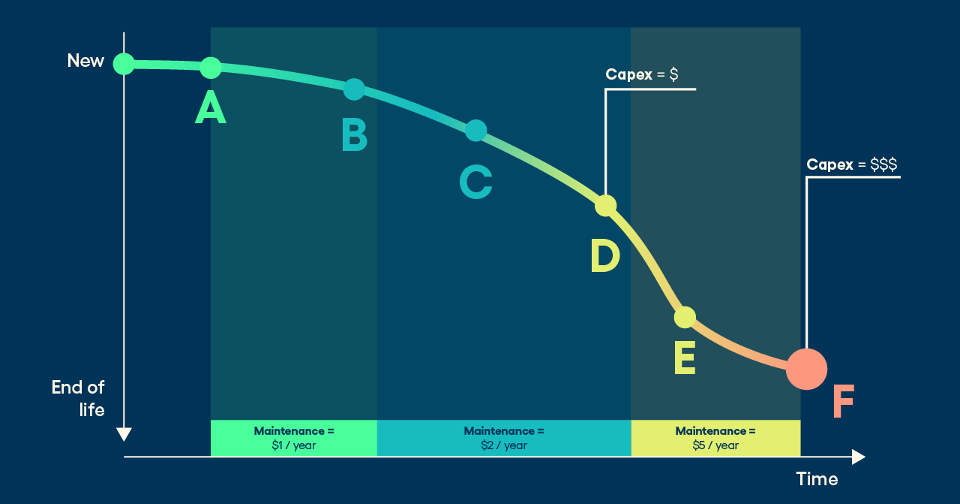
Business Problem Based on research conducted by Aberdeen, unforeseen breakdowns of equipment can incur costs of up to $260,000 per hour. These failures not only pose risks to health and safety but also highlight the need for a predictive model to anticipate potential issues. While traditional methods like routine maintenance help prevent breakdowns, they often overlook unexpected failures and may lead to excessive downtime and costs. Leveraging AI for automation enables operators to detect subtle anomalies in sensor data, ensuring maintenance is scheduled only when necessary or triggering automatic alerts when a sudden failure looms.
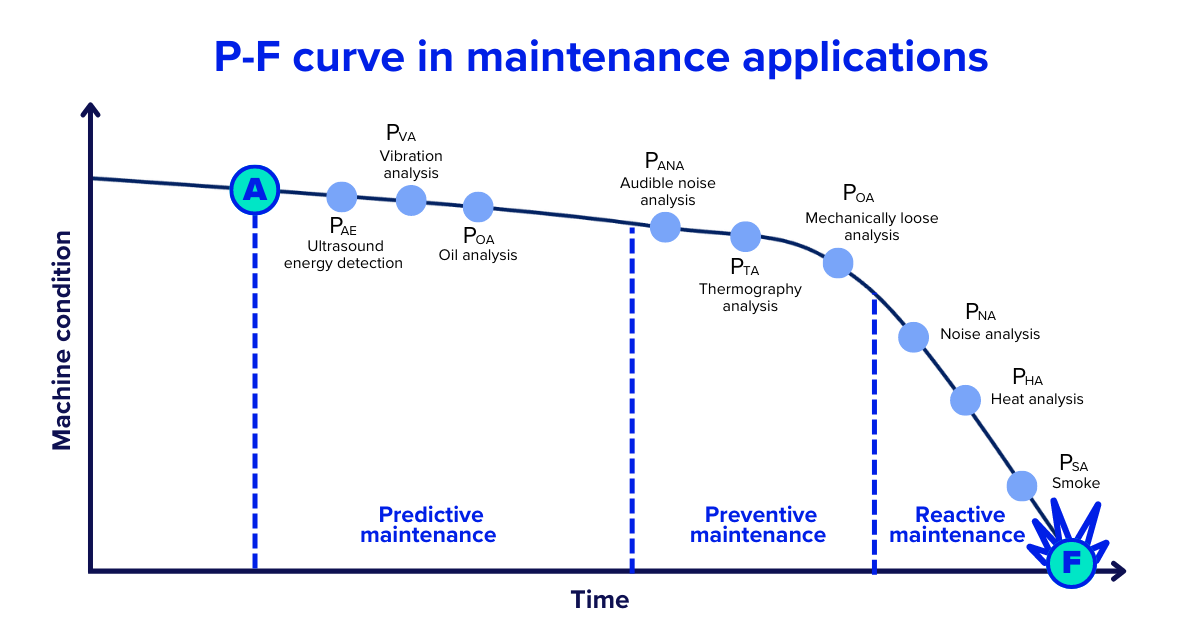
Solution
By leveraging the power of artificial intelligence (AI), your organization can revolutionize its approach to maintenance management. Through the utilization of AI algorithms, you can harness the vast amount of data collected by sensors embedded within your equipment to predict potential parts failures before they occur. This predictive capability empowers your maintenance teams by providing them with timely notifications of impending issues, allowing them to take proactive measures to address these issues before they escalate into major problems.
This proactive maintenance strategy not only minimizes unplanned downtime, which can result in significant financial losses, but also helps prevent adverse consequences such as health and safety hazards for your employees and potential damage to your inventory. By identifying and addressing potential failures early on, you can avoid costly repairs, replacements, and disruptions to your operations.
Furthermore, AI-driven maintenance solutions enable your organization to optimize its resources more effectively. By prioritizing maintenance tasks based on the likelihood and severity of potential failures, you can allocate manpower and resources more efficiently, maximizing productivity and minimizing unnecessary expenditures.
In addition to improving operational efficiency and reducing costs, AI-powered maintenance solutions also enhance overall risk management. By providing your maintenance staff with actionable insights derived from advanced data analysis, AI enables them to make informed decisions and implement preventive measures to mitigate risks effectively.
Overall, by embracing AI-driven maintenance solutions, your organization can transform its maintenance practices from reactive and costly to proactive and efficient. By forecasting potential parts failures, minimizing downtime, preventing adverse consequences, optimizing resource allocation, and enhancing risk management, AI empowers your organization to achieve higher levels of operational excellence and competitiveness in today's dynamic marketplace.
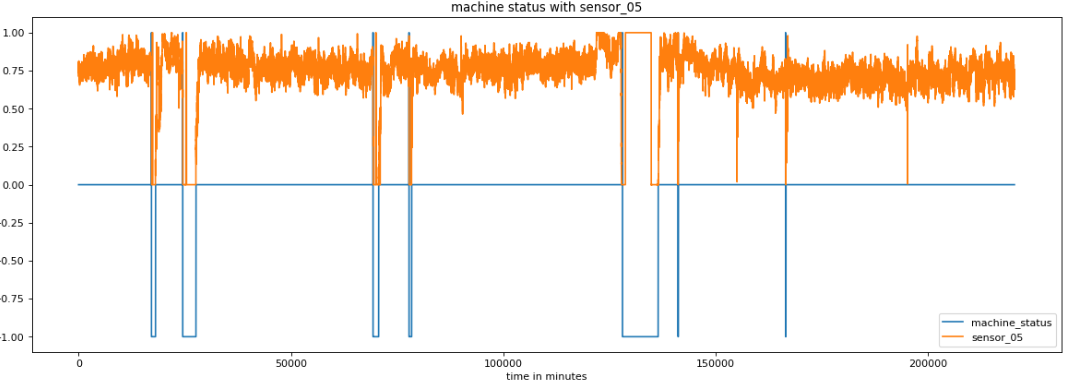
Manufacturers are increasingly turning to artificial intelligence (AI) to drive innovation and efficiency across their operations, leading to improvements in product quality, market responsiveness, and ethical standards. By integrating AI technologies into their processes, manufacturers can achieve significant enhancements in various key areas, ultimately resulting in greater productivity and profitability.
One of the primary benefits of AI adoption in manufacturing lies in its ability to revolutionize demand forecasting. By analyzing vast amounts of historical data and incorporating real-time market insights, AI algorithms can generate highly accurate predictions of future demand patterns. This enables manufacturers to optimize production schedules, minimize inventory costs, and ensure timely delivery of products to meet customer demands.
Moreover, AI-driven supply chain optimization holds immense promise for manufacturers seeking to streamline their operations and reduce inefficiencies. Through advanced data analytics and predictive modeling, AI can identify opportunities for cost savings, optimize inventory levels, and enhance overall supply chain visibility. By optimizing sourcing, production, and distribution processes, manufacturers can minimize lead times, reduce transportation costs, and improve overall supply chain resilience.
In addition to demand forecasting and supply chain optimization, AI plays a crucial role in predictive maintenance, enabling manufacturers to proactively address equipment failures before they occur. By analyzing data from sensors and monitoring equipment performance in real-time, AI algorithms can identify potential issues and schedule maintenance activities accordingly. This predictive approach not only minimizes unplanned downtime but also helps prevent costly equipment failures, thereby enhancing operational efficiency and reducing maintenance costs.
Furthermore, AI offers manufacturers valuable insights into consumer preferences and market trends, enabling them to develop products that better align with customer needs and preferences. By analyzing customer data, social media trends, and market signals, AI can help manufacturers identify emerging opportunities and develop innovative products that resonate with target audiences.
Beyond product development and supply chain management, AI also has the potential to drive improvements in ethical practices within the manufacturing industry. By implementing AI-powered monitoring systems, manufacturers can ensure compliance with regulatory standards, track supply chain transparency, and detect instances of unethical behavior such as labor exploitation or environmental violations.
In summary, manufacturers stand to gain significant benefits from harnessing the power of AI across their operations. From demand forecasting and supply chain optimization to predictive maintenance and ethical practices, AI enables manufacturers to achieve greater efficiency, agility, and competitiveness in today's rapidly evolving marketplace. By embracing AI technologies, manufacturers can unlock new opportunities for growth, innovation, and sustainable development.
Copyright © 2023 Wizio AI